INTRODUCTION
Strip cleanliness, or amount of extraneous materials (e.g., dirt, iron particles,
carbon, etc.) on the steel surface, is a key performance requirement for cold rolling
mills. Strip cleanliness is critical for mills supplying coating lines and the
automotive industry.Numerous factors from various process steps influence final strip
cleanliness. Hot mill, pickling line and annealing practices all impact cleanliness. Key
factors impacting strip cleanliness during cold rolling and their relation to specific
lubricant properties will be discussed. A short introduction to lubricant design.
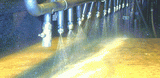
LUBRICATION
From a fundamental point of view, there are two basic performance concerns
for cold rolling lubricants. First, the lubricant usually applied as an emulsion should form
an adequate film in the inlet of the roll bite (film forma). Second, intrinsic neat oil
properties should display the desired properties (e.g., lower friction and/or reduced roll
wear).
It is widely accepted that cold rolling involves mixed lubrication, a mix of hydrodynamic or
full film lubrication and boundary lubrication.
When studying lubricant properties that impact elasto or plastohydrodynamic lubrication,
three physical parameters of the lubricant are relevant. Its viscosity (m) and
viscosity-pressure coefficient (a) are next to a number of process-related parameters such
as speeds and loads important for thickness of lubricant film. Zhang 1 et al. proposed the
film parameter MO a* as an indicator for the ability of a lubricant to form an adequate film
at the roll bite inlet. Finally, the coefficient of friction of this lubricant film, often
referred to as the traction coefficient, is an indicator of intrinsic lubricant properties.
In boundary lubrication, where film thickness is of the same order of magnitude as the
combined surface roughness, the interaction of lubricant components with the metal surface
is important. Three mechanisms can play a role: physical adsorption, chemical adsorption
(e.g., absorption of fatty acids leading to an iron soap) and chemical reactions. The key
physical parameter of the lubricant in this lubrication regime is the coefficient of
friction of the resulting boundary layer.By studying the above-mentioned lubricant
parameters in relation to the chemical structure of the lubricant, novel cold rolling
lubricants with specific, custom-tailored properties can be designed.2.
Emulsifiers play a dominant role in the performance of cold rolling emulsions as they not
only affect film formation and lubricant delivery, but also govern properties such as
emulsion stability, iron fines handling and a clean mill housing.
Various test methods are currently used to select the appropriate emulsifier package for a
certain base lubricant. Plate-out values the amount of oil (in mg/m 2 ) left on a steel
strip after spraying with an emulsion are determined and can range from 100 up to 2500 mg/m
2 . ‘Iron fines free flowing’ determines the emulsion’s ability to prevent coagulation
(clogging) of the iron fines generated in the mill. Film formation out of the emulsion can
be studied using an optical interferometer. In long-term recirculation tests, the
emulsion’s stability in time measured as the variance in particle size distribution is
established.
Factors impacting strip cleanliness, including potential impact on the selected lubricant,
are detailed in the subsequent sections.
on the strip In the cold rolling process, most iron fines are generated in
the first two stands. The amount generated depends mainly on work roll surface roughness and
the reduction schedule applied (i.e., the higher the surface roughness and the more
reduction taken in the first stands, the more iron fines are generated). Coupled mills have
an advantage they can run with lower surface roughness in the first stand, as the danger of
bite refusal is negligible compared to standalone mills.
In view of relatively low speeds and relatively higher surface roughness in the first
stands, the dominant lubrication regime will be boundary lubrication. The lubricant should
fulfill a number of requirements to reduce the amount of iron fines on the strip.
Good boundary lubricant properties are essential to lower friction and avoid excessive work
roll wear. Furthermore, the emulsion should have sufficient detergency to wash iron fines
off the strip and keep them dispersed in the bulk emulsion. Wash-off and ‘iron fines free
flowing’ are key properties that should be considered in proper selection of an emulsifier
package.
AMOUNT OF OIL ON THE STRIP
The amount of oil found on the strip at the exit of the cold mill is mainly governed by
two emulsion properties. Plate-out at a given concentration and temperature determines how
much oil is delivered to the strip from the emulsion. Wash-off determines how much oil is
removed from the strip by the emulsion. Proper selection of surfactant type and amount can
adjust the resulting balance.
From a practical point of view, the amount of iron fines on the strip has a much larger
impact on strip cleanliness than the amount of oil on strip for both full-hard and
as-annealed product.
LUBRICANT / METAL SURFACE INTERACTION
Interaction of various raw materials and formulated products was studied via
a reciprocating wear tester, originally developed by the Georgia Institute of Technology in
Atlanta. This boundary tester (Fig. 1) determines lubricant interactions with actual strip
and work roll materials. The lubricant can be studied in neat or emulsion form at
temperatures up to 400°C, and the coefficient of friction can be continuously monitored
over a relatively long period of time.
In Fig. 2, a number of base lubricants mineral oil, a natural ester and two synthetic esters
were studied using the reciprocating wear tester. The coefficient of friction (COF) was
recorded in each cycle. The coefficient of friction of mineral oil was substantially higher
(0.14 to 0.15) than the coefficients of friction of the respective esters (0.10 to 0.12).
Esters are much more polar than mineral oils and adhere much tighter to the metal surface.
As a result, the corresponding boundary layer gives rise to a lower coefficient of friction,
although details of the mechanism are not yet fully understood.
With the help of these techniques, detailed studies of individual lubricant components and
interaction effects between components can be conducted to lower a formulation’s
coefficient of friction.
Temperature influences boundary lubrication in a number of ways. Chemical reaction
rates increase two to threefold with every 10°C increase. As a result, boundary layers are more
quickly built at elevated temperatures. This is especially relevant for EP/AW additives, where the
phosphor or sulfur component reacts with the metal surface forming a low-friction boundary layer.At
higher temperatures, the activation energy for this reaction will be reached earlier.Coefficients of
friction decrease with increasing temperature as a result of increasing molecular mobility.
Lubricant molecules can absorb so much energy that they desorb from the metal surface at a critical
temperature, leading to a steep coefficient of friction increase.
Several of these temperature effects are shown in Fig. 3. The coefficient of friction decreases at
higher temperatures due to increased molecular mobility. Furthermore, one of the two lubricants
apparently desorbs at 100°C, leading to a steep increase in friction.
INFLUENCE OF STEEL STRIP HARDNESS
Most cold mills produce a range of products with quite different
metallurgical properties. In practice, the type of material rolled often impacts strip
cleanliness. As described above, the interaction of lubricant components with the metal
surface is highly relevant to boundary lubrication. The impact of similar rolling oil
formulations on different materials was studied
Various process, material and lubricant parameters impact strip cleanliness. Key factors
that impact strip cleanliness in the cold rolling process were discussed in detail.
Furthermore, theoretical considerations and laboratory results showed how each of these
factors can be influenced by proper choice of lubricant properties. As the automotive
industry continues to require steel mills to develop high-strength, light gauge materials
with improved strip cleanliness, the design and selection of lubricant properties will become
increasingly important
|